Technology that makes
the impossible possible
Innovative ideas
for the burr-less processing of heat sinks
Let’s take a look at a case we had with heat sinks for devices.
In a normal process, the heat sinks are punched and then deburred using tumbling barrels. This method allows the mass production of heat sinks without any quality issues.
However, on one occasion, we received a very challenging request.
It was from a customer who was seeking heat sinks that do not generate burrs and is free of surface abrasions.
There was also little time until the delivery deadline.
The customer sought our assistance in the hopes that we would find a solution and establish a system of mass-producing the requested heat sinks.
Requests to manufacture products without burrs and abrasions were to be expected;
however, for this particular case, the customer would not even allow the fine surface abrasions caused by the tumbling barrels during an ordinary process.
The only solution was to approach the request with a completely different process.
During the course of development, instead of challenging how not to create abrasions during the barrel processing, we focused on seeking the technology that would allow us to process the heat sinks without generating burrs.
We tried various methods, but we were unable to come across a solution that would fulfill the requirements of cost, delivery time, and quality.
Then, we saw a sliver of hope.
In an ordinary punching process, the material is punched out from one direction to the other, and it was natural for burrs to be generated in the direction of the punch.
To prevent this burr from forming, we devised a method of punching from both sides.
idea was inspired by the process of clinching in which the materials are only punched halfway, instead of being completely punched out.
We thought that there would be no burrs if we knocked out the material from the opposite direction after it was punched halfway.
In running with this idea, we still had to explore the ways to account for the difference in size between clinched products and heat sinks.
There was no guarantee that we would be able to achieve the quality we envisioned.
As it turned out, the quality was as close as it can be to our goal.
After making fine adjustments, we were finally ready with a prototype that satisfied the customer’s requirements.
Delivery time became an issue.
If we were to begin preparations for mass production at this point, we would not have the products completed by the deadline.
Enomoto’s solution was to mass-produce the heat sinks using the prototyping facilities. Normally, these facilities are equipped with the assumption to accommodate the production of 20,000 to 30,000 units.
We were faced with the challenge of mass-producing over 100,000 units in the same facility.
We operated our production day and night to meet the deadline; at the same time, we also increased the frequency of inspections, in comparison to our normal processing routine, to maintain the quality level.
As a result, we succeeded in achieving the cost, delivery, and quality required by the customer.
This technology has come to be known as the push back method and is often utilized for processing materials without forming burrs.
Compared to previous processes, the push back method has enabled us to achieve quality improvement as well as cost reduction as a result of reducing the deburring process.
It is an old but new technology, created from the innovation and craftsmanship of engineers who strive to satisfy customer demands.
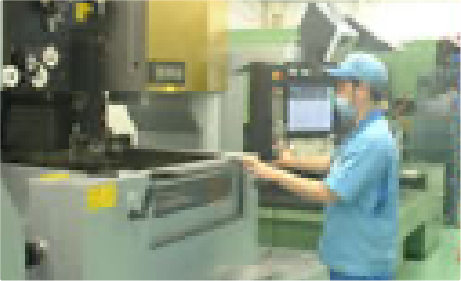

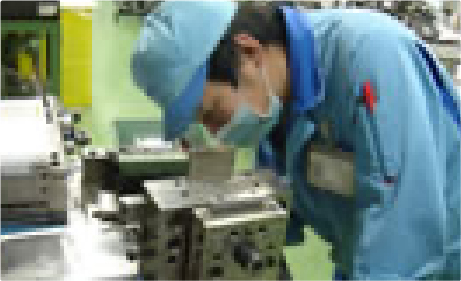